3D Printing Phoenix AZ is a process of layering material one at a time to create a 3-dimensional object. Oftentimes called rapid prototyping, it reduces design cycle times significantly.
The wide variety of compatible polymer materials enables manufacturers to quickly build and test prototypes before moving on to production. This allows businesses to react to changes in the market and customer demand more quickly.
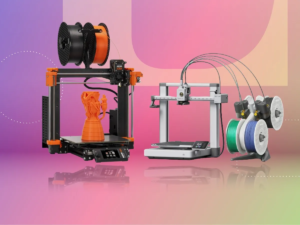
With traditional manufacturing, prototyping can be a time-consuming and costly process. However, with 3D printing, this step can be completed in a fraction of the time and for a fraction of the cost. From CAD models to physical prototypes, the entire process can be completed within a few hours, saving weeks or even months of development and testing time.
The cost of a printed prototype depends on several key factors, including the material used and the type of 3D printer. Selecting the right material is vital for producing functional, high-quality prototypes that meet your project requirements and budget constraints. Consider factors such as mechanical properties, surface finish, and chemical resistance. Also, evaluate the size and complexity of the printed object to determine if any additional materials or equipment may be required for production.
3D printing can also help reduce costs by enabling you to make changes and iterations without the need for molds or additional tools. This flexibility can significantly reduce production times, while allowing you to produce small batches of parts for testing purposes or end-use products.
In addition, the flexibility of 3D printing allows you to create a variety of physical prototypes with different properties and characteristics. For example, if you are developing an automotive or aerospace part, it is important to test the part for durability and strength. In these situations, you can use a functional prototype to simulate how the part will be used in real-world conditions and assess performance.
Another way that 3D printing can reduce costs is by allowing you to use less material than traditional manufacturing methods. This can be particularly beneficial in cases where weight is critical, such as when you need to maintain a balance between strength and speed. In these situations, you can use additive techniques to make metal parts lighter than would be possible using subtractive processes such as machining or cutting, saving both cost and time.
Lastly, you can further reduce costs by optimizing your design for 3D printing. This can include incorporating features that facilitate assembly, such as snap-fit joints and dovetails. Additionally, you can minimize material usage by designing parts to eliminate any unnecessary supports and by reducing wall thicknesses.
Enhanced Design Freedom
3D printing is a fabrication process that builds up objects from the bottom up, rather than cutting or milling them out of solid blocks (a subtractive method). This allows for complex shapes and internal lattices that would be difficult or impossible to manufacture using traditional methods. It also allows parts to be consolidated into one piece, which can reduce weight and alleviate weak joints. It also leads to greater material efficiency, which can help to cut costs.
A wide range of materials is available for 3D printing, ranging from flexible polymers to sturdy metals. This provides designers with a wide range of design options to choose from, and it helps them to create prototypes that are very close to the final product. In addition, the speed of 3D printing enables businesses to print on demand, which can reduce inventory and warehouse costs while also improving supply chain flexibility and resilience.
With digital designs, it’s easy to exchange files between project teams, facilitating better communication and more efficient collaboration. This eliminates the need to send physical files back and forth, which can be time-consuming and frustrating. It also means that companies can avoid the risks associated with physical storage and security, which could otherwise result in lost or stolen information.
Traditionally, the use of 3D printers has been limited to creating models and prototypes, but now these devices are being used to fabricate end-use products. These include tools and accessories for the construction industry, jewelry, food, shoes, and even toys. They are also being utilized by archaeologists and paleontologists to duplicate fragile artifacts.
As the technology continues to develop, it will open up a host of new possibilities for businesses. The enhanced design freedom that 3D printing offers will push the boundaries of what is possible for manufacturing. It will lead to the creation of a whole new breed of products, which will be more innovative, personalized, and customized. This will in turn drive innovation, improve business processes, and boost productivity. This will ultimately benefit the economy as a whole, while helping to create jobs in the construction industry and beyond.
Higher Quality Parts/Products
One of the biggest advantages of 3D printing is its ability to produce high-quality parts. Using this technology, engineers and designers can go from an initial concept to a fully functional prototype in a matter of days, cutting weeks out of the product development cycle. This can greatly reduce the time needed to get a new product to market and open up many opportunities for efficiency and innovation.
Using the layer-by-layer approach to fabrication, the printing process provides an extremely high level of accuracy. This ensures that each part created meets its specified requirements, ranging from intricate aerospace industry components to personalized prosthetics in medical care. This level of precision is largely due to the fact that the print process does not remove material, as is done with traditional manufacturing techniques such as injection molding and CNC machining.
All 3D printers are considered to be additive fabrication processes because they add layers of material one on top of the other rather than casting or milling them from a solid block (a consolidation process). Because they don’t have to cut and remove material, 3D printing can yield superior quality results with fewer defects and lower labor costs.
As the technology progresses, printers have become more accurate and more affordable. In addition, they can print in a variety of materials, including plastic, metals and ceramics. The earliest printers used a stereolithography technique, while more recent models utilize laser-based or electron beam sintering technologies. These methods use precisely guided lasers to heat or “sinter” powdered material, creating a solid object from the bottom up. The resulting parts are highly accurate and durable and can even be used in end-use products.
Another recent development in 3D printing is the metal technology known as direct metal laser sintering or DMLS. This process uses a nozzle that deposits metal powder or wire onto a platform, which is then heated with a laser or electron beam to melt the powder into a solid object. The resulting prints have excellent strength and durability and can be used in many different applications, including industrial manufacturing.
Increased Flexibility
A key benefit of 3D printing is that it allows companies to produce products in smaller batches, resulting in greater flexibility for manufacturers. This means that they can respond quickly to changes in the market and customer demand, and that they can easily repurpose their 3D printing assets for new products. This agility is a huge advantage over traditional manufacturing methods, which require significant upfront investment in tooling.
The ability to create parts and products in small batches also helps to ensure that they meet quality standards. For example, it would be much harder to get accurate feedback from customers and investors on a CAD file than on a physical prototype. Additionally, if there are any flaws in the design, they can be corrected immediately without having to wait for an entire production run of the product.
In addition to providing increased flexibility, 3D printing can also help to reduce waste and environmental impact. For example, traditional manufacturing processes often use a large amount of energy. A study by the Metal Powder Industries Federation found that it takes 17 steps to manufacture a truck gear using subtractive manufacturing, while 3D printing can produce the same part in just six steps. This reduction in waste and energy consumption helps to reduce carbon emissions and other harmful pollutants in the atmosphere.
3D printing also offers a range of different durable and versatile materials. Some of the most common include polymer and thermoplastic elastomers (TPE). These flexible materials have both the durability of plastics and the elasticity of rubber. This provides a wide range of application possibilities, such as soft ergonomic handles for tools and medical devices or softer casings and covers to protect against compression and shock.
Flexible prints can also be used to create articulated joints and hinges, allowing for the creation of interactive art installations that can bend, twist, and move. This level of flexibility isn’t possible with other manufacturing techniques, and it provides a unique opportunity for brands to create innovative and creative products.
In addition to being more environmentally friendly, the flexibility offered by 3D printing can also have a positive impact on the supply chain. By enabling businesses to produce products closer to where they are needed, it can significantly reduce shipping costs and associated emissions.