Being a car accident victim is challenging enough. You have to heal, work to pay your bills and manage the frustration of dealing with insurance companies that challenge and minimize your injuries.
Whether your injuries are minor or severe, they can cast ripple effects on your life and impact your ability to work, play and spend time with loved ones. A good car accident attorney can help you increase your chances of a successful recovery. Contact Baltimore Car Accident Attorney now!
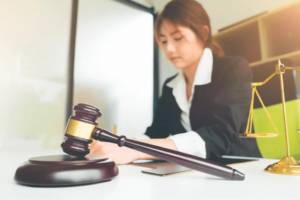
During the initial consultation, you will meet with a car accident attorney and discuss your case. They will ask questions related to your crash, your injuries, and the impact it has had on your life. They will also evaluate your claim and determine whether they believe it has a strong chance of success.
In addition to general questions about the accident, your lawyer will also want to know details of your injuries and treatment, any evidence you have gathered since the accident, and any correspondence you have had with the other driver’s insurance company. The more documentation you bring to the initial consultation, the better.
One of the most important things to remember is that you should tell your attorney everything. Even if you think the details won’t be relevant, it’s best to be as honest as possible. For example, your injury may not have immediate consequences, but over time it could cause recurring pain or other problems. In these cases, the attorney will want to be able to include those losses in your compensation request.
Your attorney will also want to know if you have health insurance because they will need to factor in any medical expenses that your health insurer has paid. This is to ensure that you are not being awarded for expenses that you would have had covered by your health insurance had you not been injured in the accident.
During your consultation, you will also have the opportunity to learn more about the attorney and their Firm. They will explain how they work, including what fees they charge and when they are due. It is crucial that you understand this information, as it will help you feel confident in their ability to represent you.
Gather Documentation
Your attorney will need to have a variety of documentation about your accident and the injuries you sustained from it. This information will help them build your case and ensure you receive the compensation you need to cover medical bills, lost wages, and pain and suffering damages.
The most important documents your attorney will need to review are police reports, photographs of the accident scene and vehicles involved, and witness contact information. Photographs are especially helpful because they can provide a clear visual representation of the accident and its circumstances. They can also highlight key details like skid marks, traffic signs, and the location of the accident.
You should also bring any medical records related to the crash, including doctor’s notes, prescriptions, and physical therapy reports. These documents will show the severity of your injuries and establish that they were caused by the accident. They will also help your attorney understand your ongoing and future medical needs.
Repair estimates and invoices will also be helpful because they translate your damages into quantifiable costs. They will help your attorney prove the amount of money you have spent on car repairs, replacement parts, and labor. You should also keep a detailed journal to document your injuries and their impact on your daily life.
Finally, your attorney will need to see your insurance policy details, including your deductibles and coverage limits. They will also want to see proof that you have been paying your premiums on time. Keeping copies of your payment receipts or bank statements will make this much easier. These records will help your attorney determine which expenses might be covered under your policy. They can then pursue compensation from the party responsible for your accident.
Keep a Journal
Car accidents are sudden, traumatic events that can turn your life upside down in the blink of an eye. Despite modern safety features and other state and federal laws that aim to prevent them, they still happen all too frequently. They can leave victims with debilitating physical injuries, thousands of dollars in repairs or medical bills, lost income due to missed work, and emotional distress such as post-traumatic stress disorder (PTSD).
An experienced car accident attorney can help you get back on your feet and pursue compensation for all your losses, including the cost of a new vehicle, lost wages, medical expenses, and other costs related to the crash. In addition, a lawyer can protect your rights when dealing with insurance companies, which are incentivized to undermine or reject your claim or lowball your offer.
A car accident attorney will review your case and all documentation you provide, such as a police report of the incident, photos or videos taken at the scene, damage to your vehicles, skid marks on the road, weather conditions, traffic and lighting, and witness contact information. They will also assess the extent of your injuries and what kind of compensation you may be eligible to receive based on your losses.
The timeframe to resolve a car accident claim can vary greatly depending on the complexity of the case. However, a car accident lawyer can speed up the process and ensure all essential steps are taken. They can also provide guidance and support through the difficult legal process while you recover from your injuries.
Don’t Assume You Can’t File a Claim
Car accidents can be frightening events. They often cause severe injuries, resulting in large medical bills and even lost income from being forced to miss work. In addition, navigating insurance laws is difficult and frustrating. That is why it is important to hire a car accident attorney.
When selecting an attorney, look for one with a good reputation and has extensive experience handling car accident claims. Take the time to review their online case results and read testimonials from previous clients. You should also be sure to ask about their fee structure, including whether they operate on a contingency basis or charge an hourly rate.
An experienced lawyer can help you navigate the complexities of the law, while fighting for a fair settlement from the at-fault driver’s insurance company. They can also protect you from making statements to the insurance company, either verbally or in writing, which can be used against you later.
Another reason to hire an attorney is if the at-fault driver has insufficient insurance coverage to cover your damages. A skilled attorney can determine if you have UIM coverage on your own vehicle to increase the amount of compensation you receive.
A car accident can be a life-changing event, especially in a city like New York. You may be struggling to recover from your injuries, juggling medical bills, and attempting to pay the rent. A skilled lawyer can take some of the burden off your shoulders so you can focus on healing. Contact us for a free consultation. We are committed to helping our clients get the best possible outcome in their cases. We have over 15 years of experience fighting for victims in St. Louis and beyond.
Don’t Delay Filing
Getting the compensation you deserve for your car accident injuries is an important priority. A qualified car accident attorney will have the experience and resources to ensure your claim is filed correctly, processed on time, and resolved in your favor. They are also familiar with various deadlines and will keep track of all the necessary paperwork for your case. This will ensure your case is not delayed or lost due to missed deadlines.
The next phase in the process is gathering supporting evidence to build your case. This may involve obtaining and reviewing medical records, police reports, eyewitness statements, and other available documentation. If needed, your lawyer will consult with experts to assist in the investigation, such as accident reconstruction specialists and medical professionals. They will use this information to draft a demand letter that clearly states your injuries, expenses, and losses.
After building your case with the help of supportive evidence, an experienced car accident attorney will negotiate to receive a fair settlement. If a fair settlement cannot be reached during negotiations, your lawyer will prepare to present the case in front of a judge or jury. They will be your advocate in the courtroom, ensuring that your voice is heard and your rights are protected.
You should always feel comfortable discussing your case with an experienced car accident attorney and be able to ask questions at any time. The more you know about the process, the better. It is also important that you and your attorney communicate regularly, so that you can be updated on the status of your case. Depending on the stage of your case, you may hear from them a few times per month or every day.